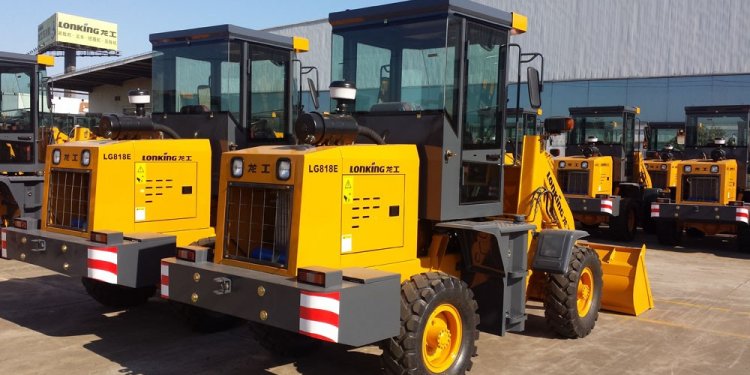
Best Wheel Loader
Depending upon your operation, trade-offs may exist in selecting the best wheel loader configuration for load-out vs. performing other tasks on your construction sites. Typically, three to four passes is the most efficient match to load on-road trucks.
Balancing the loader to the frequency of trucks is really where you gain efficiency. “Whatever the number of passes, if you load a truck as another one shows up, you are at optimum efficiency, ” says Gary Bell, vice president/general manager, KCMA Corporation, manufacturer of Kawasaki wheel loaders.
The optimum number of passes really depends on your operation. “Caterpillar has advocated three to five passes as optimum for pit loaders and rigid-frame trucks operating in shot rock, ” says Don Weinhold, wheel loader product application specialist. “In a yard application (loose, stockpiled aggregate), the target is typically three passes.”
However, he notes, “The actual pass match varies significantly due to the wide range of on-highway truck capacities.”
Cycle times between most wheel loaders are typically the same. Most stockpile loading applications vary from 25- to 45-second cycles. This would be pretty constant regardless of the number of passes. This cycle time should be balanced with the capacity and availability of trucks.
Trade-offs Required
The need for versatility creates trade-offs in terms of optimum capacity.
“Unlike the pit loader, a yard loader works with many different products (gradations of material) each day, ” says Weinhold. “Different products have different densities and can cause wheel loader payload to vary dramatically. For example, clean, washed 1/2-in. limestone aggregate may have a density of 2, 500 lbs./cu. yds. Base material at the same site may have a density of 3, 000 lbs./cu. yds.”
Base material will also include a large amount of fines. “Washed materials have lower fill factors (90% to 95%) in a wheel loader bucket, and base materials have high fill factors (110% to 120%), ” Weinhold points out. “The net result is a dramatic difference in the payload the wheel loader achieves when loading the different materials. In the pit, the loader works in material that has relatively consistent density and bucket fill factor.”
While yard loader operators are well aware of this difference, many others in the aggregates industry make the incorrect assumption that yard and pit loaders experience similar and consistent material densities and fill factors. In order to achieve maximum loader efficiency and durability, the difference must be understood by the machine owner.
“Wheel loader manufacturers design machines based on a nominal working payload and loading cycle profile, ” says Weinhold. “Exceeding these design targets can have a significant impact on machine durability.”
Choose Buckets Wisely
There are some basic questions that you have to ask no matter what you are loading. “The first thing is the density range of the material, ” says Chad Ellis, product specialist, Doosan. Next is the bucket size. “Then we put a machine up under there that can handle it.”
One of the most common mistakes is the sizing of the buckets. “There is a tendency to just get the machine size they think they need and use a standard bucket, ” says Ellis. This can negatively impact productivity. “That can be overcome by starting with the density of the material and the size of the bucket you need before you pick the machine.”
Examine your options. “We have several bucket sizes based on the material densities, ” says Richard Iddins, Volvo Construction Equipment. “Sometimes it takes some data to get the right bucket. You start by asking what production they are looking for at the end of the day. How many tons do they want to get out? Next is material density and bucket size. Then you get into machine size.”
Carefully consider truck flow through the site. “Some applications have a constant flow of trucks. Then there are other applications where you can’t always control the amount of time in between trucks, ” says Ellis. “If you have consistency in trucks, it is not that difficult to figure out what you need. But you do need to look at long term. In the long term, what is the site going to look like? Are we talking about a permanent spot or something that is moving?”
Be cautious about the true limitations of bucket size relative to material density and wheel loader capacity. Some customers try to gain an advantage by using a larger bucket. Bell has witnessed this firsthand over 45 years in the industry. “If they had a 3-yd. loader, they wanted to make it a 3 1/2-yd. loader somehow, ” he comments. “If they had a 4 yd., they wanted to make it a 4 1/2 yd. People are always trying to push these machines beyond their capability.”
Overloading a machine accelerates wear. “If you sell a smaller machine to do the same work, you can sell a customer a lower cost per ton, at least in the purchase price and probably most of the operating cost, ” says Bell. “But if you ask a machine to take 20% more, it will probably last 20% less overall. It does not make sense that you can do 20% more work and not wear the machine out more quickly.”
Of course, operating costs are going to escalate as the machines grow larger. “A larger machine burns more fuel, ” says Ellis. “Look at the fuel burn vs. the actual productivity that you are getting out of it. Just the cost of maintenance — tires cost more on a bigger machine. The whole overall hourly cost is more the larger the machine that you get.”
When versatility and speed trump size
Poland Sand and Gravel, Poland, NY, has a large product base, offering 20+ products. Its wheel loaders have to perform multiple functions around the jobsite with operators shuttling machines to where they are needed.
“There is a lot of movement in our operation. We need good travel speed and good acceleration, ” notes Scott Rommel. “Our piles are spread out.”
The wheel loaders have to perform a variety of tasks including load-out, carry and stockpile. “Being quick around the pit is important, ” says Rommel. “In order to be quick around the pit, you need a decent ride and a feel of stability. In addition, we are running up and down slopes because we are essentially a hillside operation.”
The company’s wheel loader fleet currently consists of a Doosan DL500, DL450, DL400 and Komatsu 380, along with a few smaller loaders for cleanup. “We started out with 3- and 4-yd. loaders, ” says Rommel. “Now, we are up to a 5-yd. machine with the 400, the 500 is 6 3/4 yds. and the 450 is right in between. It is probably a 6 1/4-yd. machine the way we have it set up with our cutting edge on it.