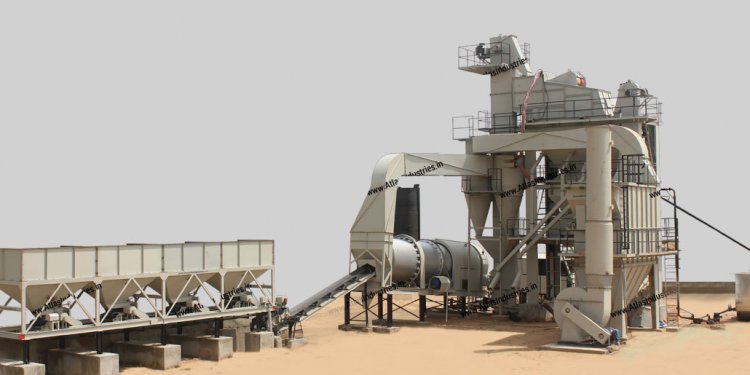
Asphalt batch Mix plant
By Ed Misajet
Fred Prill doesn’t pull any punches when the subject of new batch plant facilities is brought up in conversation. “Very few contractors with the exception of some in the extreme northeast are interested in batch plants anymore—at least not new ones, ” states Prill, an equipment consultant with decades of experience working with leading asphalt plant manufacturers. “Batch plants, in their time, were the state of the art, very functional, and met the needs of most asphalt producers.”
Batch plants, used at the turn of the century, were simple in design. A one-ton batch plant (60 tons per hour [tph]) was the typical size. The quality of the mix generated by these plants met the specifications of the day. However, the quality of the mix produced was manually controlled by the skills of the plant operator. The primary requirement in the early days was for the aggregate to be completely coated with liquid asphalt. These needs were reflected in the plant’s design. A typical batch plant was equipped with a hopper or bin to introduce the aggregate, a small dryer to heat the stone, hot screens to separate the aggregate into several sizes, weigh hoppers to control proportioning and a pugmill to blend the asphalt cement (AC) and aggregate.
Needs Changed
As time went on, the needs and requirements changed and batch plant design grew more complex. During the 1950s, interstate construction required hot mix asphalt (HMA) contractors to increase production capability. Typical batch plant size increased to six tons to meet production demands. Larger screens were added to accommodate the production of multiple mixes. Otherwise, batch plants changed little until about 30 or 35 years ago.
The major changes that followed were the onset of automatic computer batching controls, more efficient dust collectors and the emergence of surge silo systems. Plants got a lot bigger and cleaner. They added silos to minimize truck turnaround time. But plants still produced one batch at a time. Expensive pugmill mixers and multideck screens were still required. They resulted in high initial costs plus high maintenance costs, which were the batch plant’s ultimate downfall.