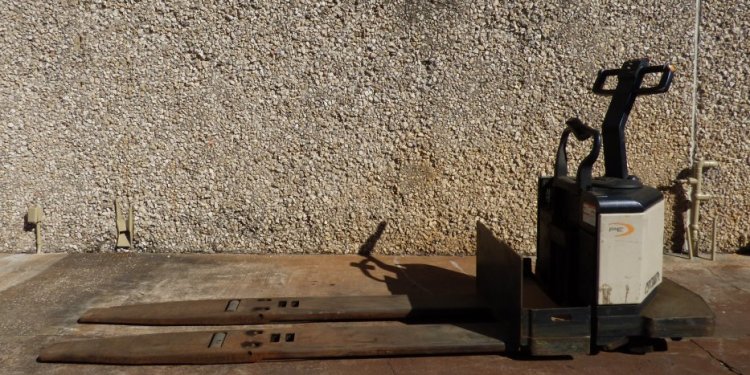
Crown Double Pallet Jack
Introduction
This article discusses a relatively new technology that is now being experimented with and deployed within high volume distribution center operations in Europe and the United States. The concept involves driverless mobile equipment (pallet jacks or forklifts) such that order selectors no longer need to get on and off of the vehicle as part of the picking process. This is emerging as an exciting new opportunity to improve the safety, ergonomics and productivity associated with full case order picking which is the most labor-intensive job in many distribution operations.
In this article we review two companies (Kollmorgen and Seegrid) that have developed two different solutions for driverless mobile equipment. The technologies differ in their design and approach but they are both generating interest within industries that are characterized by labor intensive full case picking operations. We expect that you will be hearing significantly more about these solutions over the next decade.
Background Information
If you have ever witnessed a conventional high volume full case distribution center then you can appreciate just how hard the job of order selection can be. Without doubt, full case order picking is one of the most physically demanding jobs in the distribution industry because operators must repetitively lift and stack heavy cases of merchandise throughout the work day. In many distribution centers, it is not unusual for an order selector to pick 15+ tons (i.e. 30, 000+ pounds) of product during a normal work shift.
Order picking often accounts for 40 – 45% of the direct labor force within a distribution center. It is the job of the industrial engineer to balance the trade-offs between maximizing order picking productivity; building high-stability outbound pallets; and ensuring work place ergonomics and operator safety. To this end, many companies have implemented some form of solution to improve order selection productivity including: slotting; voice directed picking; ergonomic pick racks, engineered labor standards; and incentive systems. These solutions have been widely deployed in companies in developed countries over the past 15 years.
Aside from full blown automated order picking, the price tag of which is out of reach for the majority of companies, the time is ripe for something new to advance labor efficiency for conventional distribution operations. Enter the concept of driverless lift trucks and pallet jacks with the intelligence to travel throughout the pick line and to/from the dock without the need for human intervention. We believe that this technology provides a relatively affordable solution that delivers a strong return on investment for improving the productivity, ergonomics and safety associated with high volume full case picking operations.
Kollmorgen - Pick-n-Go
Kollmorgen Corporation is a large global manufacturing company specialized in motion systems and components for original equipment manufacturers (OEMs). Kollmorgen’s parent company is Danaher Corporation headquartered in Washington DC. Kollmorgen’s headquarter is located in Radford, VA.
Kollmorgen has a long and established reputation as being a leader in the motion industry with product lines that include motors, drives, controls, gearheads, linear positioners and power generation. Specific to the material handling industry, Kollmorgen is an established leader in the automated guided vehicle (AGV) market with 15, 000 AGVs deployed across 1, 000 sites around the world over the past 35 years. Kollmorgen also produces many of the standard drives, controllers, motors, gears, etc. that go into forklift trucks, monorails, AS/RS, and conveyor equipment so the company is already well-established within the material handling industry.
We recently spoke to Tomas Angervall, Product Marketing Manager AGV Systems for Kollmorgen in Sweden. In 2006, the company developed a driverless forklift product branded as Pick-n-Go® which is best described by video at the following link. The concept behind Pick-n-Go is that the order selector no longer needs to get on and off of truck during the full case picking process because the vehicle is continually self-directed to move in advance of the operator. Similarly, when the pallet is complete, the driverless forklift truck automatically transfers the pallet to a designated location on the shipping/staging dock and concurrently a new driverless truck with an empty pallet arrives such that the operator can continue working. The net effect is the elimination of wasted time getting on and off the truck and driving to and from the dock. As we will illustrate later on in this article, this is not only worth some serious money, it is also a safer and more ergonomic approach to traditional full case order selection
Depending on the size and type of distribution operation where this technology application is deployed, Kollmorgen has indicated that labor order selection productivity gains of between 25% to 100% are achievable. Kollmorgen claims that their clients are consistently achieving a return on investment typically within 24 months. Clearly, larger distribution centers with labor-intensive full case picking operations are the main target candidates for this type of solution.
In short, here is how the Kollmorgen solution works:
- There is a one-time engineering set up required to prepare the warehouse for the Pick-n-Go solution. The facility needs to be prepared to support one of the multiple navigation techniques offered by Kollmorgen. Since laser navigation tends to offer the best performance, this article focuses on that approach.
- A special reflective tape is placed on rack uprights throughout the distribution center. Typically these are placed 20 to 30 feet apart such that every 2nd or 3rd rack upright has a reflector on it. The idea is that the laser technology always knows where the vehicle is within the facility by reflecting the laser off of the reflective tape. When racks are not available, the tape is placed onto building columns...